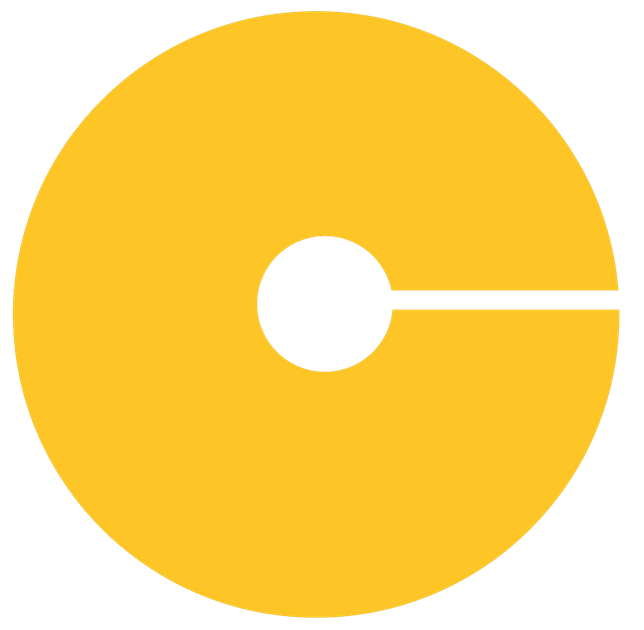
- …
- …
HARDENING SERVICES
High Bar Vacuum
Up to 12-Bar Vacuum Hardening
Our high pressure quench vacuum furnaces incorporate thorough and uniform convection assisted heating along with directional cooling of up to twelve times atmospheric pressure. The results are excellent distortion control with superior quenching rates, which provide the highest quality vacuum heat treated products available in today’s marketplace.
Equipment:
Vacuum furnaces accommodates parts up to 38" x 36" x 50"
Vacuum furnaces with an increased hearth zone with a capacity of 6,600 lbs.
Vacuum Bright Annealing & Tempering
The vacuum draw furnaces heat and cool through a high velocity circular wind flow pattern which provides exceptional heating and cooling temperature uniformity. All tempering processes are computer controlled to provide consistency and accuracy load after load. The surface integrity of parts is maintained throughout the entire draw cycle which results in vacuum bright parts.
Salt Bath
Deep Salt Bath
Century Sun continues to lead the thermal processing industry with the modern installation of its long length hardening line custom engineered, designed, and built to accommodate parts fully immersed to 110" in length. This liquid molten salt bath hardening line is the largest of its kind for the quench and temper of tool steels, high speed steels and powder metallurgy. Experts in the hardening and straightening of long length tools, Century Sun continues to emerge as the leader for the thermal processing of specialized tooling within the heat treating industry.
Equipment:
- Salt bath hardening furnaces accommodate parts up to 24” x 36” x 110”
- Precision temperature control up to 2250 °F
- Salt bath draw furnaces accommodate parts up to 30” x 40” x 110”
THERMALTUFF®
THERMALTUFF™ is a precisely controlled heat treating process using molten salt baths resulting in optimum metallurgical properties that increase value by extending the life of tools that manufacture parts through hot forming and hot forging operations. This accelerated salt bath quenching process yields the highest impact toughness attainable in hot work die steels with minimal distortion.
Carburizing & Carbonitriding
Case Hardening
Super Allcase® hardening line with computerized control systems. Load size of 36" x 36" x 48" with a maximum capacity of 3000 lbs. Superior quench rates and temperature uniformity results in consistent case depths and uniform hardness.
Computerized CASEmate® control systems provide repeatable quality load after load. High performance gas system controls shallow or deep case requirements.
Equipment:
Super Allcase® atmosphere controlled integral quench furnaces and tempering furnaces accommodate parts up to 36" x 36" x 48".
Materials:
All alloy grade materials suitable for hardening, carburizing, or carbonitriding can be processed in this department. Attention is given to proper fixturing to ensure uniformity in hardness and case depths. Select areas can be masked off in order to comply with the customers part specifications.
Induction Hardening
INDUCTION HARDENING
Power supplies range from 100 kW to 450 kW at frequencies from 3 kHz to 30 kHz and provide case depths from .060" to .500" deep. The microprocessor stores and recalls on demand specific programs to ensure quality and repeatability of process. We have the ability to custom design and build induction coils to reduce lead times and control costs. From full harden, quench and temper to just end tempering and drawbacks, Century Sun is equipped to handle your induction hardening needs.
Equipment:
- Twin spindle dual power supply vertical induction scanners that accommodate parts ½” diameter to 13“ diameter x 60” long
- Horizontal induction scanners that accommodates parts 1” diameter to 8” diameter x 150” long
- Induction deep case capabilities from .060” depth up to .500” deep
Ion Nitriding
Ion nitriding has wide applications in several alloy steels, tool steels, and high speed steels. It is reliably repeatable—part after part. Tools may be hung vertically from the top or loaded on the hearth plate, with an overall capacity of 6,500 lbs., 60" diameter, and 72" height.
ION NITRIDING
This is the high-tech advancement in nitride processing, through the use of vacuum technology, exacting computer controls and gas mixing techniques. A case hardening process dramatically increases the wear resistance of tools, while significantly improving corrosion resistance. The vacuum process not only leaves surfaces clean, but also minimizes dimensional distortions.
At specific temperatures and electrical voltage levels, nitrogen gases are ionized and impregnated into the compound layer as iron nitrides. The control of temperatures, voltage and amperage, and gas mixtures, work together to create the depth of penetration and degree of hardness optimal for the intended uses of the workplace.
Equipment:
- Long length ion nitride process furnaces accommodates parts up to 30” diameter by 96” length
Ion nitride bottom load process furnaces accommodate parts up to 50" x 50" with a hearth capacity of 6,000 lbs. each.
CASETUFF® & CASEWEAR®
CASETUFF™ is a deeper, more ductile ion nitrided layer which resists heat checking and improves the thermal fatigue resistance of hot working dies. Typical applications include hot forging dies, cast tooling, molds, etc. Consistent results demonstrate that the CASETUFF™ processes add significant value by extending tool life.
CASEWEAR®
CASEWEAR™ is a precisely controlled ion nitrided case (70+ RC) that increases tool life of high speed steel cutting tools and cold working dies. Typical applications include broaches, end mills, stamping dies, etc.Request a Quote
Please click the button below to get a quote.